High-quality stainless steel automatic preparation unit multi function chemical dosing system for Chemical Industry Wastewater Treatment
- Model
- Dosing system
Review
Description
Dosing System
Categories: Dosing System
Brand: AquaSust
Warranty of core components:5 years
Core Components:PLC
Place of Origin:Zhejiang, China
Warranty:2 years
Productivity: 500L/Hour/100L/Hour/10000L/Hour/250L/Hour
Weight (KG): 100 kg
Weight: 100kg
Net water: 2(m3/h)
Turbidity of inlet water:500(mg/l)
Turbidity of effluent:3(mg/l)
Material:Carbon Steel / Stainless Steel
Application: Solid-liquid Separation
Delievery time: After get the deposit within 15 days
Usage: wastewater pre-treatment
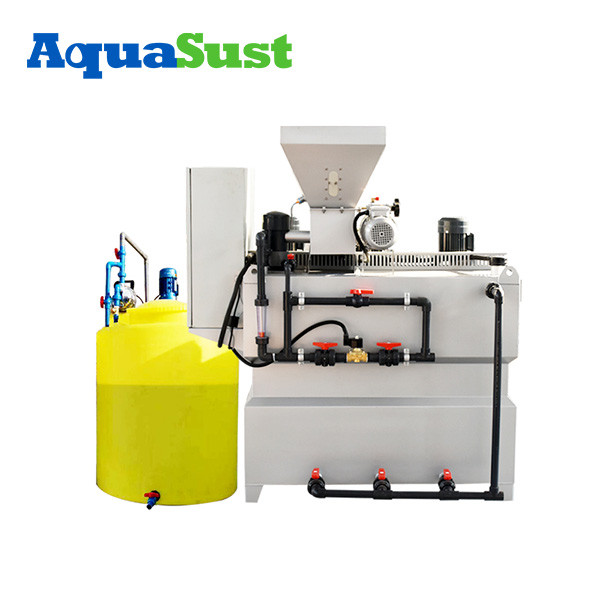
Dosing System Advantages:
"Dosing System" i.e. quantitative dosing system, is mainly used for precise control and distribution of the amount of liquid or gas, which is widely used in chemical, pharmaceutical, food and water treatment industries. The product advantages of this type of system can be described in the following aspects:
1,Precise control: Dosing systems enable precise control of the amount of chemicals to be dosed, ensuring that chemical reactions in the treatment process take place as expected, thus improving product quality and consistency.
2,Cost saving: Through precise dosing of chemicals, waste of chemicals can be minimised, while reducing the safety issues and additional treatment costs that can be caused by over-dosing.
3,Automated operation: Most dosing systems are equipped with advanced automated control systems that can operate automatically without human intervention, improving operational efficiency and reducing labour costs.
4. Easy integration: Modern dosing systems are designed to be flexible and can be easily integrated into existing industrial production lines to work with other automation equipment.
5. Improved safety: Automation and precise control reduces the need for operators to come into direct contact with chemicals, thereby reducing health and safety risks in the workplace.
6,Environmentally friendly: Accurate chemical dosing helps control emissions and waste, meets environmental standards and reduces environmental pollution.
7,Customisability and Expandability: Many manufacturers offer customisable solutions to meet the needs of specific industrial applications, while the design of the system allows for future expansion and upgrades.
These advantages make the ‘Dosing System’ very popular and necessary in many areas, especially in industrial processes that require precise mixing and dosing of chemicals.
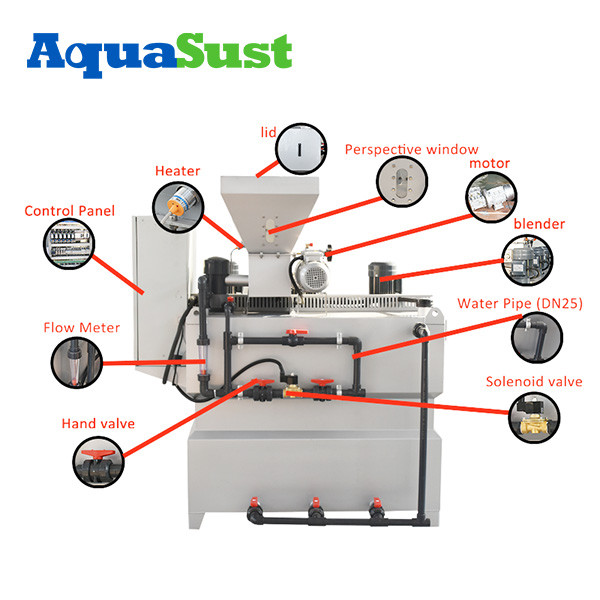
Dosing System Working Principle
The principle of operation of dosing systems is based on a mechanism for accurately controlling and dosing a variety of liquid or gaseous chemicals. These systems typically include several key components such as pumps, controllers, sensors, and injection devices that work in tandem to ensure precise and continuous chemical delivery. The following is a detailed explanation of the basic principles of operation:
1,Pumping Device: The pump is the heart of the dosing system and is usually a diaphragm pump, piston pump or peristaltic pump. The role of the pump is to draw the chemical from the storage container and push it in a controlled manner to the target point of the system.
2,Control System: The controller is the brain of the system, responsible for receiving data from the sensors and automatically adjusting the pump speed and operating cycle according to the set dosage or programme. The controller can be a simple manual setting or a complex microprocessor-based automatic control system that can dynamically adjust parameters according to real-time data.
3, Sensors and monitoring equipment: Sensors monitor key parameters such as flow rate, pressure, pH, conductivity, etc. throughout the dosing process. This data is sent to the controller to ensure accurate and timely adjustments to the dosage.
4, Injection Points and Mixing: Chemicals are piped to injection points, usually specific locations in the process, where they can be most efficiently mixed with the treatment medium (e.g., water). In some systems, a mixer may also be included to ensure that the chemical is adequately mixed with the treatment medium.
5,Feedback and Adjustment: The system continuously collects feedback data by means of continuous monitoring, from which the controller adjusts the pump's operating parameters in response to changes in actual conditions or to meet preset treatment criteria.
6, Safety and Alarm Systems: Most modern dosing systems are equipped with safety features and alarm systems to prevent system overloads, chemical spills or other potential operational problems.
This system design not only improves the efficiency and safety of chemical use, but also increases the safety level of the entire work environment by reducing direct operator contact through automated controls. Because of their efficiency and precision, dosing systems are used in a wide variety of industrial and environmental applications where precise control of chemical dosing is required.
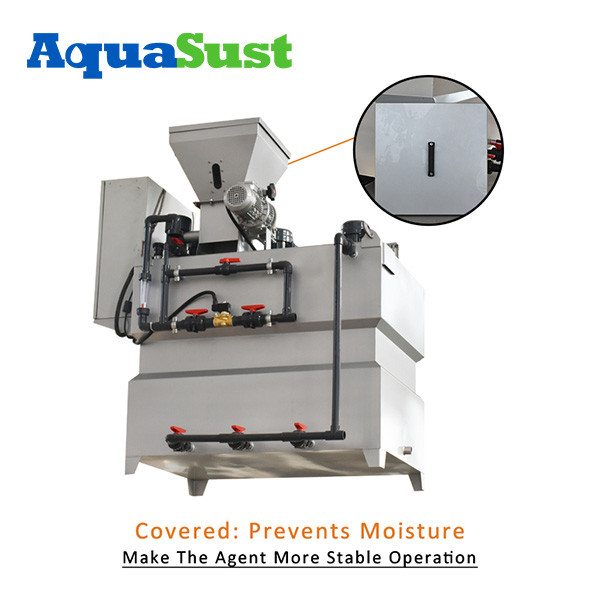
Dosing system in Chemical Industry Wastewater Treatment Application
1. Precise chemical dosing
Chemical wastewater usually contains complex pollutants, which need to be treated with a variety of chemicals (such as flocculants, coagulants, acid-base regulators, oxidizers and disinfectants, etc.). The dosing system can accurately control the dosage of chemicals to ensure stable treatment effect and avoid wastage of chemicals and side effects caused by over dosage.
2. pH adjustment
The pH value of chemical wastewater may fluctuate greatly, through the dosing system can accurately add acid or alkali, quickly adjust the pH value of the wastewater to the appropriate range, to provide stable water conditions for the subsequent treatment process. This is especially important for the biological treatment process, because the appropriate pH value is essential for the activity of microorganisms.
3. Promote flocculation and sedimentation
Chemical wastewater contains a large number of suspended solids and colloidal substances, the dosing system can accurately add flocculants and coagulants to promote coagulation and sedimentation of suspended solids and colloids, significantly improve the solid-liquid separation efficiency, reduce the load of the subsequent treatment unit, and improve the quality of the effluent water.
4. Remove organic matter
Chemical wastewater contains a large number of organic substances, the use of dosing system adding oxidizing agents (such as hydrogen peroxide, potassium permanganate, ozone, etc.) can effectively degrade organic pollutants, reduce chemical oxygen demand (COD) and biochemical oxygen demand (BOD), improve the biochemistry of the wastewater, and enhance the efficiency of the subsequent biological treatment process.
5. Removal of heavy metals
Chemical wastewater may contain various heavy metal ions, the dosing system can add appropriate precipitants or complexing agents, so that heavy metal ions form insoluble precipitates or complexes, removed by precipitation or filtration, thus reducing the concentration of heavy metals in the wastewater to meet the discharge standards.
6. Control foam
During chemical wastewater treatment, especially in the aeration and biological treatment stage, a large amount of foam may be generated. The dosing system can add anti-foam agent to control the generation of foam, maintain the normal operation of the treatment facilities and avoid environmental pollution and equipment damage caused by foam overflow.
7. Disinfection treatment
In the final stage of wastewater treatment, disinfection is usually required to ensure that the effluent water quality meets the standard. The dosing system can accurately inject disinfectants (such as chlorine, sodium hypochlorite, ultraviolet light, etc.) to effectively kill pathogenic microorganisms in the wastewater and ensure the safety of the effluent.
8. Improve treatment efficiency and stability
By accurately controlling the dosage and dosing time of chemicals, the dosing system can significantly improve the efficiency and stability of the wastewater treatment process. Avoid the fluctuation of treatment effect and equipment failure caused by improper dosage of chemicals, and ensure the long-term stable operation of the treatment system.
9. Reduce operating costs
The automatic control of the dosing system can reduce manual operation and lower labor costs. At the same time, accurate dosing of chemicals reduces the waste of chemicals, reduces the cost of chemicals and improves the overall economic efficiency.
10. Monitoring and optimization
Modern dosing systems are usually equipped with automatic monitoring and data recording functions, which can monitor various parameters (such as pH value, redox potential, flocculation effect, disinfectant concentration, etc.) in the process of wastewater treatment in real time, and optimize the dosing strategy according to the monitoring data to further improve the treatment efficiency and effluent water quality.
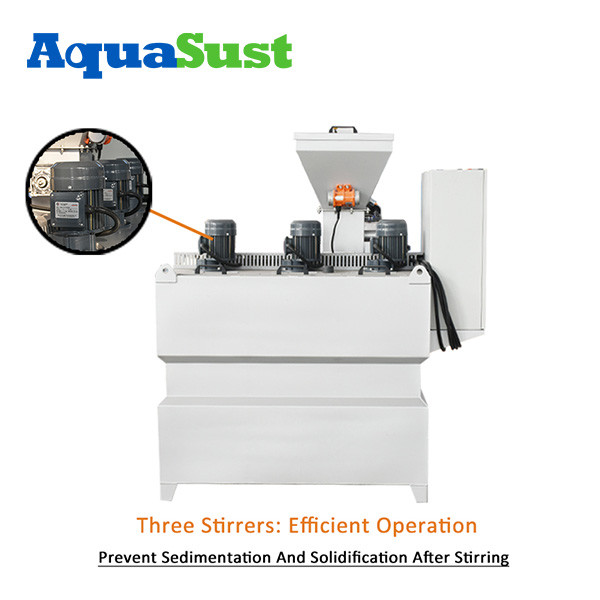