Vortex Blowers for Chemical Industry Wastewater Treatment
- Model
- AS-RB-2/4
Review
Description
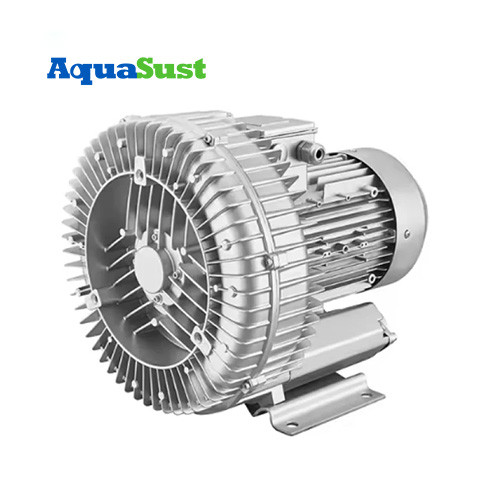
Aquasust Vortex Blowers
Vortex blowers are devices used to generate airflow or gas pressure, also known as vortex blowers or vortex fans. They use the kinetic energy of the vortex to convert into pressure energy, rather than relying on traditional impeller or centrifugal force. Vortex blowers typically consist of one or more rotating blades that operate similarly to a turbocharger, generating vortex kinetic energy by introducing gas or air into the rotating blades. The vortex kinetic energy is then converted to the pressure energy of the gas, creating the desired airflow or gas pressure. This design allows the vortex blower to provide high mechanical efficiency and low energy consumption for a variety of industrial and commercial applications requiring gas transport or pressure boosting.
Vortex Blower Performance Parameters
Vortex Blowers Feature:
1. High efficiency and energy saving: The scroll blower adopts the principle of converting vortex kinetic energy into pressure energy, which has high mechanical efficiency. Compared to traditional rotary vane blowers or centrifugal fans, scroll blowers are generally able to provide the same air volume and pressure with lower energy consumption.
2. Low noise: Due to their simple structure and low rotational speed, scroll blowers produce relatively low noise during operation. This makes scroll blowers particularly suitable for applications requiring low noise environments, such as indoor air handling systems.
3. High reliability: scroll blowers have no lubricants, turbines, gears or other wearing parts, and therefore have a long service life and low maintenance costs. Their simple construction and small number of moving parts also means relatively low failure rates.
4. No Oil Pollution: Scroll blowers do not require lubricating oil to lubricate the rotating parts, so there is no oil pollution problem. This makes scroll blowers particularly suitable for applications with high environmental requirements, such as food processing and medical equipment.
5. Compact size: scroll blowers usually have a compact structure and take up less space. This makes them able to provide sufficient air volume and pressure despite limited space, which makes them more flexible and convenient in design and installation.
Aquasust Vortex Blowers in Chemical Industry Wastewater Treatment Application
1. Aerobic biological treatment
In an aerobic biological treatment unit for chemical wastewater, a vortex blower ensures that there is sufficient dissolved oxygen in the system by providing sufficient airflow to promote the growth of aerobic microorganisms and the degradation of organic matter.
2. Membrane Bioreactor (MBR)
In MBR systems, the vortex blower provided by the scroll blower not only helps oxygen transfer, but also reduces membrane contamination, extends membrane life and improves the treatment efficiency of the MBR system.
3. Aeration tank
In the aeration tank, the vortex blower improves the oxygen transfer efficiency by generating uniform bubbles, ensuring that organic matter and pollutants in the wastewater are fully degraded and improving the treatment effect of the aeration tank.
4.Sludge treatment
In the sludge treatment process, the vortex blower promotes aerobic stabilization and dewatering of sludge by providing airflow, improving sludge treatment results and reducing sludge volume and treatment costs.
5. Wastewater homogenization tank
In the wastewater homogenization tank, vortex blower are used to maintain uniform mixing of wastewater, prevent precipitation of suspended solids, and improve the treatment efficiency of subsequent treatment units.