MBBR Mixer for Sludge tanks
- Model
- AS-MIXER5.5/4
Review
Description
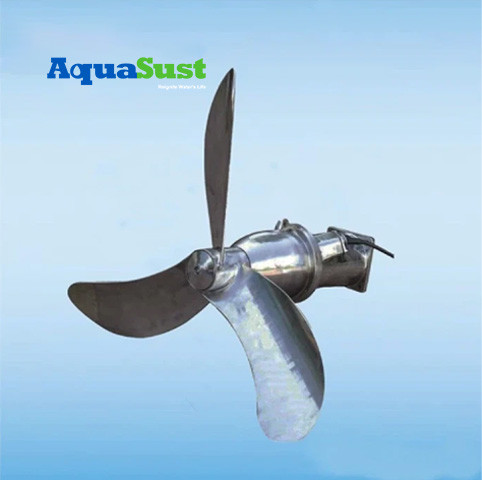
Low Speed Mixer Performance Parameters
Model
|
Power (KW)
|
Electrode | Rated Current (A) |
Speed (R/Min)
|
Quantity (Set) | Diameter (Mm) | Threst (N) |
Weight (Kg)
|
AS-MIXER3/4 | 3 | 4 | 6.6 | 420 | 2 | 400 | 1400 | 75 |
AS-MIXER4/4
|
4
|
4 | 8.6 |
420
|
2 | 550 | 1800 |
85
|
AS-MIXER5.5/4
|
5.5
|
4 | 11.8 |
420
|
2 | 550 | 2100 |
90
|
AS-MIXER7.5/4 | 7.5 | 4 | 15.5. | 420 | 2 | 620 | 2600 | 100 |
AS-MIXER11/4
|
11
|
4 | 24 |
420
|
2 | 750 | 3100 |
120
|
AS-MIXER15/4 | 15 | 4 | 33 | 420 | 2 | 800 | 3500 | 150 |
Aquasust MBBR Mixer Feature:
1.Lower Impeller Speed: The mixer has a lower impeller speed, only 106 revolutions per minute (r/m), compared to the typical 400 to 1000 r/min of a submersible mixer. This slower speed, approximately 10 to 20% of the typical speed, is tailored to meet the specific process requirements of the bio-carrier tank.
2.Large Diameter Three-Leaf Blades: The mixer features large diameter three-leaf stainless steel blades. This design is carefully selected to meet both hydraulic and biocarrier process requirements within the tank. The size and material of the blades contribute to efficient mixing and durability, important factors in wastewater treatment systems.
3.Self-Cleaning Propeller: The propeller is designed for self-cleaning functionality. Constructed from stainless steel material, it not only ensures durability but also incorporates features for automatic cleaning. This design consideration enhances the longevity and effectiveness of the mixer in maintaining optimal performance over time.
4.Versatile Installation System: Equipped with an installation system developed by Aquasust, the mixer can be installed on the equipment from multiple angles. This flexibility in installation enables efficient and adaptable integration into various configurations of the bio-carrier tank, optimizing space utilization and overall system effectiveness.