What are the design points and usage precautions of MBR process?
- Share
- Issue Time
- Feb 10,2025
Summary
In traditional wastewater biological treatment technology, mud-water separation is completed by gravity in the secondary sedimentation tank, and its separation efficiency depends on the sedimentation performance of activated sludge.
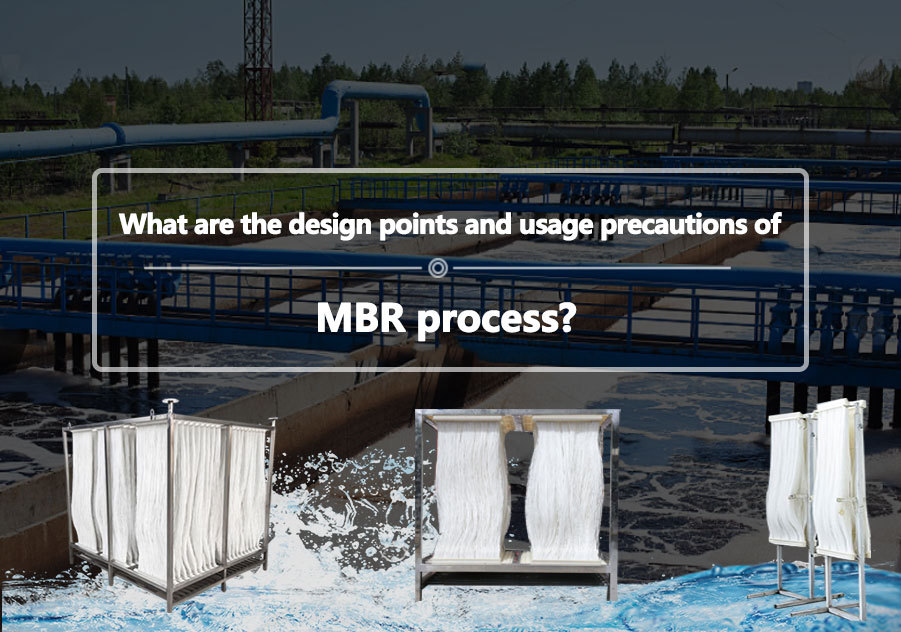
What are the design points and usage precautions of MBR process?
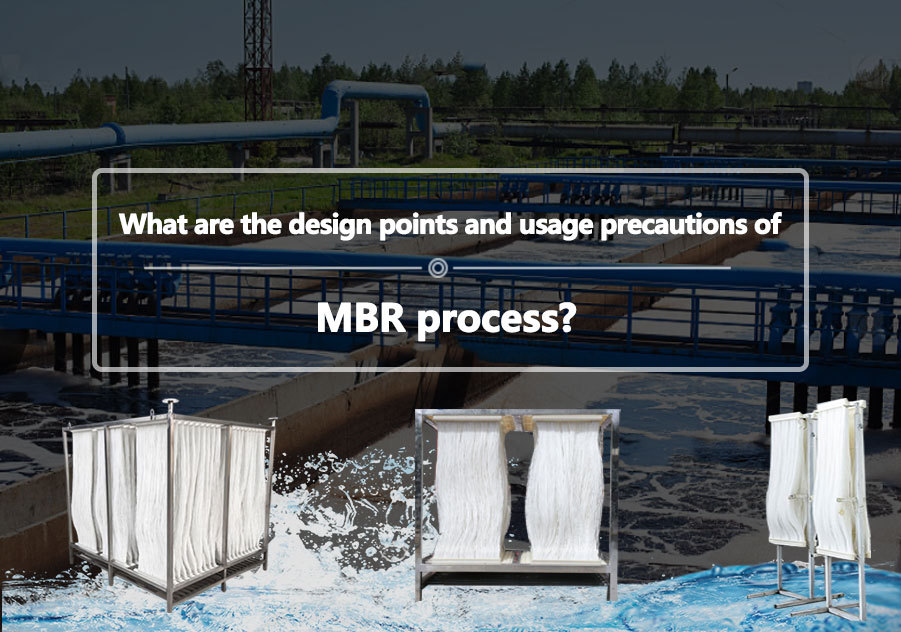
In traditional wastewater biological treatment technology, mud-water separation is completed by gravity in the secondary sedimentation tank, and its separation efficiency depends on the sedimentation performance of activated sludge. The better the sedimentation performance, the higher the mud-water separation efficiency. The sedimentation performance of sludge depends on the operation status of the aeration tank. To improve the sedimentation performance of sludge, the operating conditions of the aeration tank must be strictly controlled, which limits the scope of application of this method. Due to the requirements of solid-liquid separation in the secondary sedimentation tank, the sludge in the aeration tank cannot maintain a high concentration, generally around 1.5~3.5g/L, which limits the biochemical reaction rate. The hydraulic retention time (HRT) and the sludge age (SRT) are interdependent, and increasing the volumetric load and reducing the sludge load often conflict. The system also produces a large amount of residual sludge during operation, and its disposal cost accounts for 25% to 40% of the operating cost of the sewage treatment plant. The traditional activated sludge treatment system is also prone to sludge swelling, the effluent contains suspended solids, and the effluent water quality deteriorates.
In response to the above problems, MBR organically combines the membrane separation technology in separation engineering with the traditional wastewater biological treatment technology, greatly improving the solid-liquid separation efficiency; and due to the increase in the activated sludge concentration in the aeration tank and the emergence of bacteria in the sludge (especially dominant bacteria), the biochemical reaction rate is improved; at the same time, by lowering the F/M ratio, the amount of residual sludge produced is reduced (even to 0), thus basically solving many outstanding problems existing in the traditional activated sludge method.
1. Is the wastewater suitable for MBR membrane method?
MBR is not a panacea. It belongs to microfiltration membrane and is defined by the particle size that can pass through it. Therefore, the clogging problem is the key for it. It is recommended not to use MBR membrane method for some wastewater that is easy to scale, contains oily substances and viscous substances.
Wastewater types that are not suitable for MBR method include: emulsion/grinding liquid/quenching liquid/cooling liquid wastewater, surfactant wastewater, petroleum wastewater, lipid wastewater (except for pretreatment measures).
2. Design points of MBR aeration device
(1) The aeration device can be fixed on the bottom of the pool (it needs to make a membrane component support frame and a membrane component slide rail), or it can be made together with the membrane component. Each has its own advantages and disadvantages. The position of the aeration pipe should be carefully considered. DN20 perforated pipe is used. Each membrane gap corresponds to a perforated pipe. The perforation size is Φ2.0mm, and the perforation spacing is 100mm. The perforations of adjacent two pipes are staggered. The orifices are made in a single row vertically upward. There are many double-row and oblique downward methods. I personally think it is not advisable. The settled sludge will not block the orifices.
(2) A rough estimate of the aeration volume is made. According to empirical data, the ratio of soda to water is 24:1 (conventional pool depth is 3.5m). The fan exhaust pressure head is selected to be 0.01Mpa higher than the highest liquid level. A vent valve is set at the fan outlet. The vent pipe can discharge 70% of the air volume when the vent pipe is fully opened. A muffler is installed on the vent port. This device is used to control the DO value in the biochemical tank and protect the fan.
(3) A separate control valve should be made for aeration, and a microporous oxygen aeration device should be used to ensure that the stirring air can be flexibly adjusted. Quantity and oxygenated air volume;
(4) The optimal DO control of the MBR pool is between 2.5 and 5. The normal liquid level is about 3ppm. When the liquid level is different, the DO will also change. It is not advisable to exceed 5.0ppm for a long time
3.Design considerations for MBR membrane components
(1) Assemble the membranes together to form a membrane component. Pay special attention to the fact that the distance between the membranes should be large enough and the effective distance should be greater than 100mm (the axis distance is greater than 140mm). If the membrane fibers of the membrane itself If the density is high, the effective spacing should be appropriately widened. The purpose of this is to keep the flushing airflow smoothly reaching the top membrane wire, reduce the hardening and interception between the membrane wires, and reduce the cleaning frequency of the membrane assembly;
The spacing of the flat membrane only needs to be 60~80mm; too large a spacing will cause too much space to be occupied;
(2) The membrane can be installed horizontally or vertically, depending on the installation space; when installed horizontally, the membrane wire is kept slightly drooping, and the droop amplitude is kept at 10mm. In other words, it is necessary to keep the membrane wire as straight as possible while ensuring that the membrane wire is not subjected to tension, so that there will not be too much debris between the membrane wires; vertical installation is recommended;
(3) The membrane assembly cannot be made too large, because a membrane assembly that is too large will have a large installation density, and the same amount of stirring air is insufficient for it. Moreover, when a lot of wrapped materials accumulate on the membrane, the membrane needs to be sprayed with a high-pressure water gun or tap water. If the installation is too dense, it will be difficult for you to flush the inner membrane. It is recommended that the processing capacity of a single membrane assembly should not exceed 1.5m3/hr;